his year, Vaucher Manufacture Fleurier celebrates 20 years in business. The company owes its existence to the wealthy Sandoz Family Foundation which, in the late 1990s, set about building an ambitious and comprehensive watch division with Parmigiani Fleurier at its centre, rapidly followed by Atokalpa (Alle), acquired in December 2000, then Les Artisans Boîtiers (La Chaux-de-Fonds) in May 2000, Elwin (Moutier) in January 2001 and Quadrance & Habillage (La Chaux-de-Fonds) in December 2005.
Since its arrival in April 2019 as Chief Executive of Vaucher Manufacture Fleurier, Jean-Noël Lefevre has implemented with success what he calls, in managerial language, “operational excellence”. Lefevre is no newcomer to the industry. After graduating in mechanical engineering and management, followed by prolonged stints at automotive suppliers (where efficiency gains are key), in 2006 he joined Cartier as logistics manager before moving to Roger Dubuis as director of production. He was appointed CEO of Manufacture Stern 1898 then spent three years as production manager at the Vacheron Constantin factory in Le Brassus before taking up his position of CEO at Vaucher Manufacture Fleurier.
Armed with operational solutions, Jean-Noël Lefevre says that sales have doubled and production volume increased fourfold between 2019 and 2022, 2023. This “change in dimension”, he says, kicked in during 2022 – no doubt the time required for his measures to take full effect.
Lean manufacturing
This “operational excellence”, as practiced by the new CEO, revolves around a horizontal organisational structure whose purpose is to promote greater transparency between objectives, operational decisions, necessary adjustments, initiatives and… the wellbeing of employees. A firm believer in “modern managerial methods” and lean manufacturing, Jean-Noël Lefevre is building a manufacturing tool based on trust and engagement. Employees form dedicated units which are given autonomy to manage tasks or “projects” and organise their part of production. Workstations are shared and employees are expected to take charge of more than one operation within the unit.
At the same time every morning, without fail, each unit stands in front of a whiteboard for a meeting that lasts 10 to 15 minutes. These daily check-ins serve to collectively outline objectives, areas and means for action, as well as quality issues that concern the workshop. Everyone takes responsibility, everyone takes action.
Information is centralised on a main chart that monitors work in progress… not with a complex system but using a simple, visual method of coloured cards that anyone can consult. Products in various stages of completion are tracked with complete transparency at every stage in production, from numerically controlled machining to quality control, from logistics to contracting.
“It takes several months of discussion to set up each autonomous unit,” explains Jean-Noël Lefevre. “Employees are directly involved in designing their unit. The aim is to collectively improve the production situation, reduce work in progress and cut down production times.”
The customer is the ultimate target and their satisfaction takes priority. But to achieve this, “the well-being of each employee is at the heart of every process.” Pay equity (externaly audited) is the rule. The environment is also a focus. Photovoltaic panels have been installed on the roof and the Manufacture is a member of the Swiss Triple Impact directory.
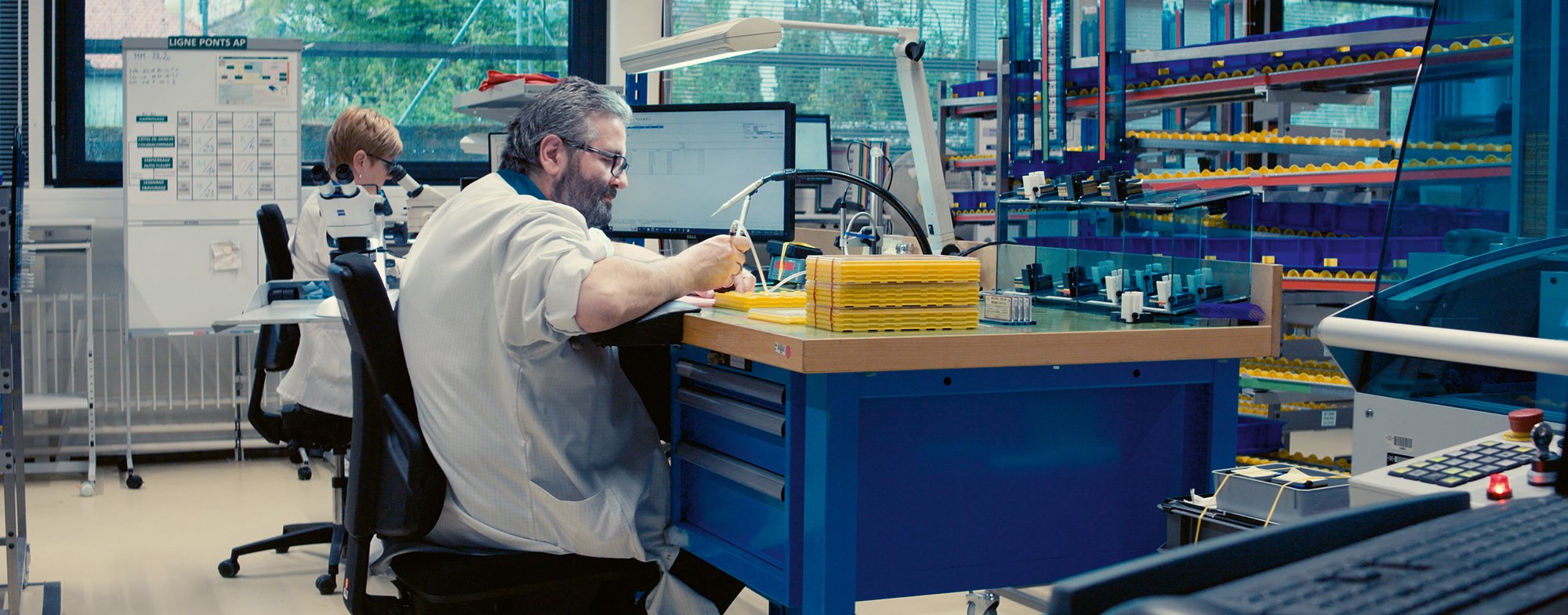
Guided tour
Inside the Manufacture, the atmosphere is peaceful and pleasant, marked by colour, transparency and a hum of background noise. The CEO’s office on the top floor is next to offices for the movement constructors, designers and project managers, but also communication and IT. A glass cabin occupies the centre of this vast open space, where two people can sit and talk quietly, at any time of day, without being disturbed. On every floor, wood-clad coffee stations provide further opportunity for employees to meet and socialise.
Across 5,800 sq m, 230 people work to “keep pace with growth, reduce production times and ensure the highest quality.” They represent every function: CNC operators, supply chain managers, production planners, constructors, designers, lab technicians and human resources, alongside watchmakers, movement adjustors, decorators and quality controllers.
Equipment, which is configured per production unit, is on a par: an in-line battery of Willemin 701S CNC machines, laser cutters, laser engravers, as well as flexible cobots that work alongside human “colleagues” to increase CNC productivity (“for tasks with no added value,” insists Jean-Noël Lefevre).
Employees are cross-trained and understand each stage within their unit. They are connected physically one to the other. A “hot spot” at the centre of each unit groups together the workshop manager, production and quality assurance engineers and the production planner. They form what could be described as the executive branch of this “democratic” workshop.
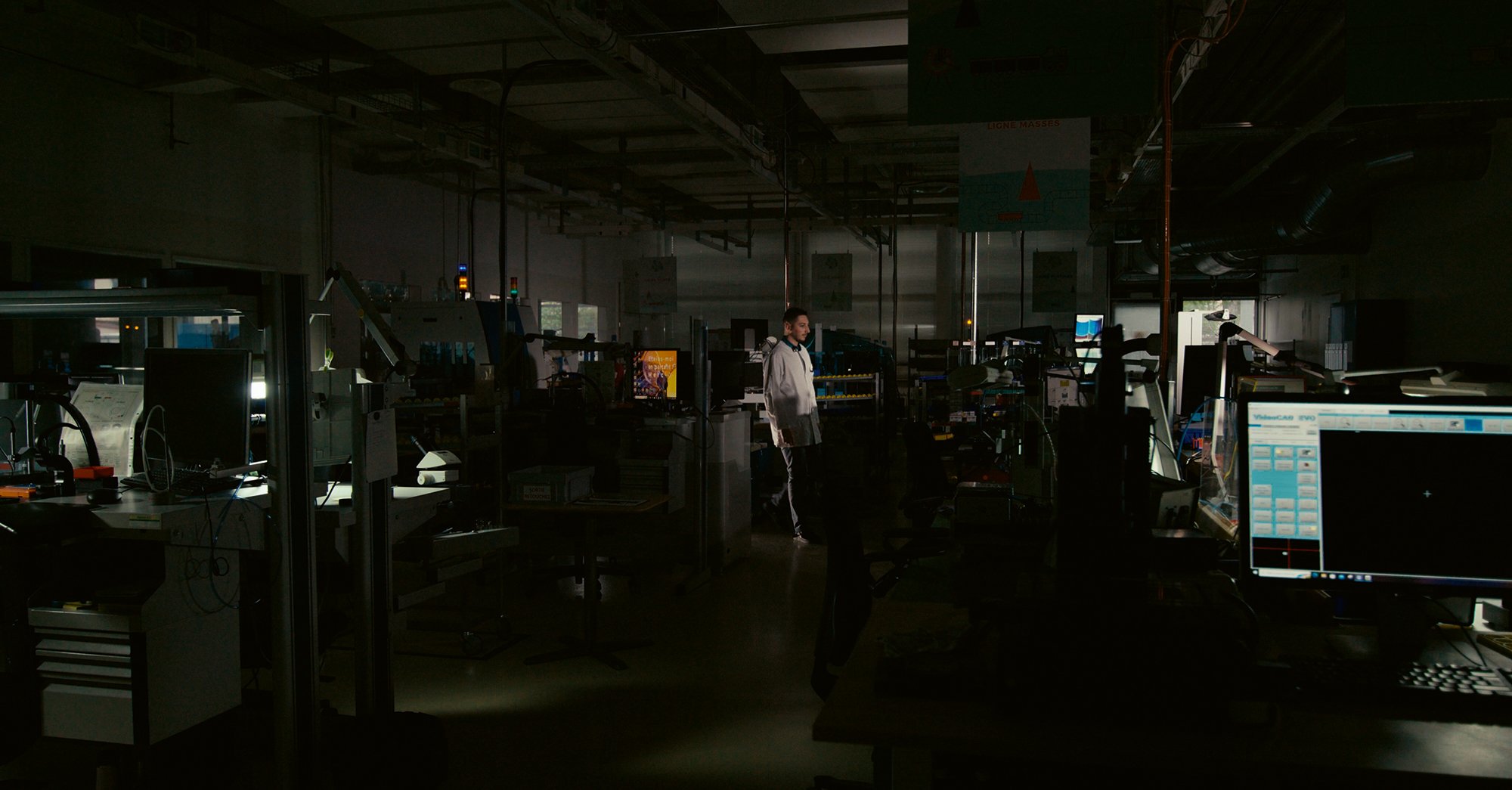
The movements
Production encompasses five base calibres: a three-hander, an extra-thin with micro-rotor, an integrated chronograph, an automatic tourbillon and a manual-winding tourbillon.
For “standard” clients, the oscillating weight and bridges can be modified on request. For “very important” clients, Vaucher Manufacture Fleurier goes further, even letting them “play with the bricks” of their calibres, sometimes to the point of rendering them unrecognisable. There is also the option to start from a blank page and develop a complete new movement: skeletonisation, colours, surface treatments, layout, form movements, et cetera.
-
- Integrated chronograph (30mm) with high-performance automatic column wheel. Calibre 6710 is the result of 6 years of development. It incorporates the best-known solutions and several innovations for optimal efficiency, reliability, precision, and robustness. Its construction combines a high-frequency balance (5Hz), a column wheel, a vertical clutch, and a linear hammer. COSC Certificate.
-
- Manual Tourbillon (30mm) Modern and innovative, the Seed VMF 5430/22 movement is one of the thinnest tourbillons in the world. The originality of its construction, its avant-garde design and great opportunities for personalisation are real assets. Flying tourbillon volant with a titanium cage Variable inertia balance with gold inertia blocks. Frequency 3 Hz (21.600 A/h)
-
- Automatic Tourbillon (28.00mm) Self-winding flying tourbillon, the Seed VMF 3024 movement has numerous advantages. Fitted with a double barrel, a titanium cage, and a variable inertia balance, it remains slim, precise and always robust. Its gold oscillating weight and exceptional finishes make it an extraordinary movement.
-
- Extra-thin micro-rotor (2.60mm - 30mm). The Seed VMF 5401 movement offers an elegant and uncluttered design that stands out for its harmonious proportions and finesse. Placed in the body of the mechanism, its micro-rotor contributes to its refined aesthetics.
-
- Classic automatic Seed VMF 3002 (23.30mm -25.60mm). With its double barrel, it delivers a more regular energy to its variable inertia balance. Thus optimised, its timekeeping can be COSC certified if requested. Robust and versatile, this movement remains elegant.
Vaucher Manufacture Fleurier probably has around thirty projects scheduled between now and 2028, at various stages of completion. We’d love to name names but, as at any other movement manufacturer, confidentiality is de rigueur. Some brands take pride in their collaboration but many more prefer to stay quiet on the matter. “I can truthfully say we are known for the quality of our production,” Jean-Noël Lefevre adds. “Yes, we are expensive but we also provide superior reliability with a return rate of just one per cent.”
We venture to ask how many movements Vaucher Manufacture Fleurier produces per year. We don’t get a straight answer, but we are told it manufactures tens of tousands movement each year and that it can also supply series of 25 pieces – a privilege no doubt reserved for its most loyal customers.
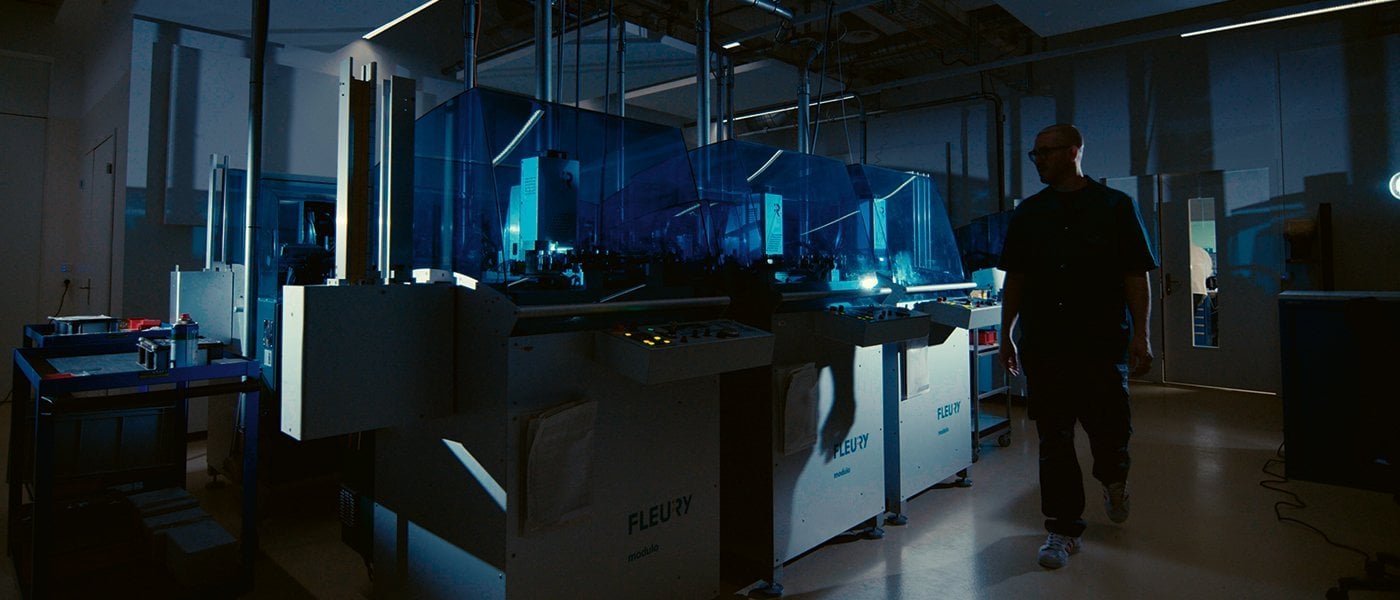