ince the beginning of the year, some big names in the luxury sector have put forward initiatives such as the production of sanitiser or masks to combat the pandemic. The aim of these temporary actions is to show solidarity in a time of crisis. For Babette Keller Liechti, the founder of Keller Trading, a Swiss supplier of microfibre products for the watchmaking industry, the outlook is quite different: her company aims to establish itself firmly in a new market: that of protective mask production.
“We are a long way from putting the health crisis behind us,” she says. “Without stricter governmental measures, the second wave will be stronger than the first, and the third will be even stronger than the second. China has been able to contain the virus because they know that the only solution is strict containment.”
Keller Trading, a Swiss supplier of microfibre products for the watchmaking industry, aims to establish itself firmly in a new market: that of protective mask production.
-
- Babette Keller Liechti founded Keller Trading for professional watchmaking products, then KT Home for personal care. The production of masks is housed in this second structure.
Being a specialist in textiles and hence a connoisseur of the longstanding tradition of mask-wearing in Asia (a continent that is very aware of the risks of a pandemic), the entrepreneur explains that she felt the danger coming when a case of an unknown virus was reported in China in mid-December 2019. “I started to find out about the possibility of producing masks with the microfibre we use for watches. I contacted the Swiss Federal Office of Public Health to find out how long the coronavirus could survive on the material, and built up new stocks of fibre.”
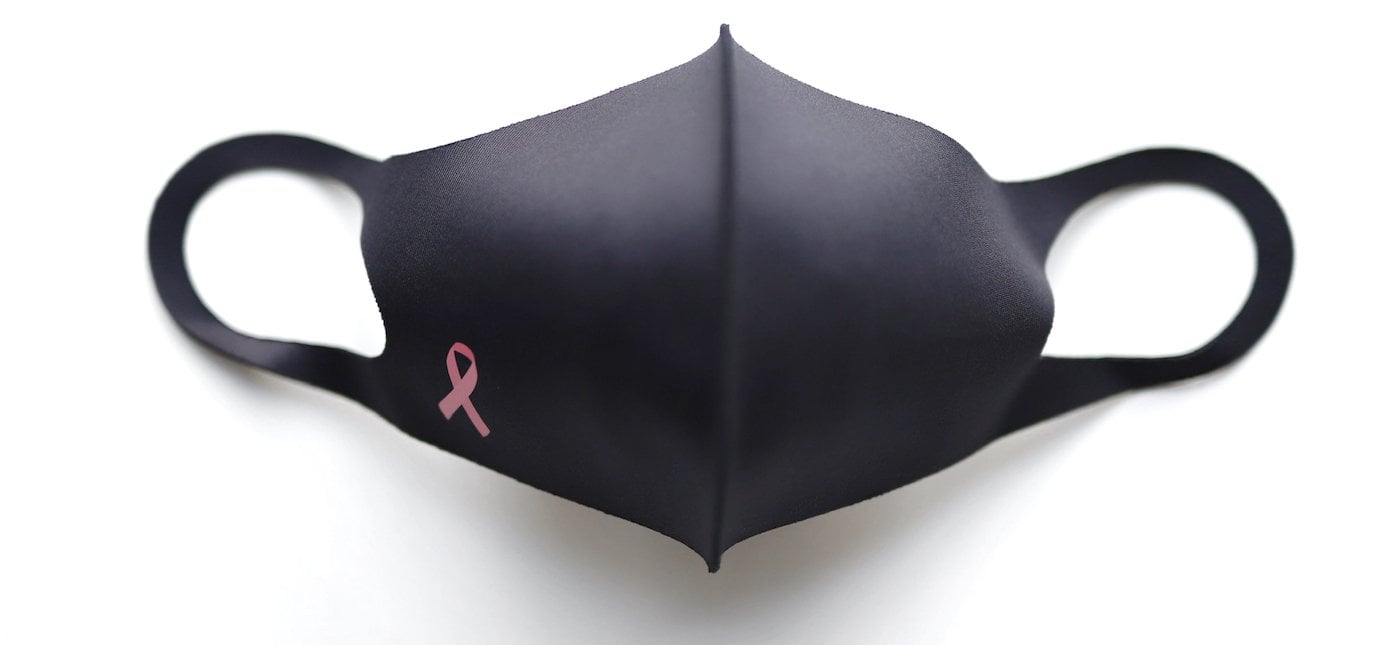
Overcoming several challenges in a new market
February: the first cases emerged in Europe, without creating much of a reaction – we all remember the debates about whether wearing a mask would do any good. Babette Keller Liechti explains that at that time she had developed 14 different mask prototypes, and had started to produce a series of them for her relatives and employees. However, the results were not satisfactory. “The microfibre didn’t form a seal against the skin, it was uncomfortable to wear and it let particles in. It wasn’t the protection I wanted.”
The entrepreneur contacted a business partner based in South Korea who also specialises in microfibres. “He provided me with several textiles, including the one that I selected. In the end, the mask is made of 90% polyester microfilaments and 10% microfilaments of silver fibre and spandex, for optimal fit.”
The first results were not satisfactory. The entrepreneur then contacted a business partner based in South Korea who also specialises in microfibres.
-
- The company offers six sizes of masks, for children and adults.
The containment measures started in March. At the same time, a website was developed and the first masks were marketed by KT Home (the personal care branch of Keller Trading). Here too, adjustments were necessary: “I started with a standard M size, but I very soon realised how much the morphology really does vary from one person to another. The mask has to protect from the bottom of the chin to the middle of the nose while allowing the skin to breathe and feel comfortable.” Six different sizes were gradually introduced, for both children and adults.
An inspiring initiative for the industry
Babette Keller Liechti thought that demand would naturally come from her existing clients: watchmakers. After all, they have to put up with long days at the workbench, which can be quite physically demanding in itself, but imagine wearing an uncomfortable mask... Her prediction proved wrong: “I have had individual watchmakers among my customers, but groups and companies have preferred to order large amounts of disposable paper masks.”
This is another perverse aspect of the virus that the entrepreneur stresses: “Politicians did not foresee such a deluge of paper masks, which has become a major factor of environmental pollution. In addition, the problems of exposure to pesticides linked to the material over long wearing times are an insidious threat. There are people who are going to have health problems, not because of Covid-19, but because of the poor quality of mass-produced masks.”
“Politicians did not foresee such a deluge of paper masks, which has become a major factor of environmental pollution.”
-
- The new Everyday 2.0 mask is certified with a filtration efficiency that exceeds 70% at a particle size of 1 micrometre.
It is to counter this double threat – medical and ecological – that Babette Keller Liechti defends the concept of Swiss masks made of microfibres that can be washed and reused (priced at around twenty francs each). That’s why she has redirected part of her staff to their production: “The aim is to offer impermeability not to breathing but to the virus, without a paper filter between the textile and the face. The filtration efficiency for particles exceeds 70% at a particle size of 1 micrometre.”
-
- Disposable paper masks, a potential ecological disaster
Sold to companies or private individuals over the internet, KT Home’s masks meet the Testex Community Mask certification, as approved by the Swiss Covid-19 task force. The textile used is certified by Koteri (South Korea) and the FDA (USA). “Over the months of October and November, we hired 20 people for the production of masks,” says Babette Keller Liechti. “Since the beginning of November, we have sold more than 30,000 pieces and sales have quadrupled since we obtained our certification mid-October.”
The production technique has been patented by the company and the machines used, each with an output capacity of 800 masks per day, are ordered from Germany. It is only a short stretch from there to conceiving of a broader conversion of the Swiss and European industrial infrastructure to manufacturing high-quality protection against a virus that is destined to become a fixture in our lives for some time to come.
Towards a broader conversion of the Swiss and European industrial infrastructure?
The entrepreneur concludes: “I invested more than CHF 100,000 in R&D for the production of masks in a time of crisis. There is still a lot of education to be done to encourage people not just to wear a mask, but to wear it correctly. Before putting a product against your face for a long time, it is worth asking yourself the question: is my mask good quality?”
This article is part of a report to be published in our print issue on 30 November 2020.