he price of rhodium is soaring. Its cost has quadrupled over the past four years and in 2020 it became the world’s most expensive metal, selling for as much as CHF 800 per gram – CHF 800,000 per kilo.
And for many reasons it is unlikely to stop there. Mined mostly in South Africa and the Russian Urals, production is no more than 20 tonnes a year, and deposits are inexorably diminishing. At the same time, demand for rhodium is exploding, mainly because of new anti-pollution measures for cars – catalytic converters, for example. But it is a crucial component in other sectors too, for the nuclear industry, for lighting, mirrors, connectivity technology and more.
The watchmaking sector is also a big user of rhodium. The whitest precious metal after silver, it is highly resistant to corrosion and does not tarnish. Fine coatings of it have been used since time immemorial to reinforce certain crucial parts of the movement – such as the ébauches – to which it gives a highly appreciated white finish.
The price of rhodium is soaring. Its cost has quadrupled over the past four years and in 2020 it became the world’s most expensive metal, selling for as much as CHF 800 per gram – CHF 800,000 per kilo.
-
- White platinum coating for movement blanks is a high-quality, innovative alternative that is far more economical than the traditional rhodium, now the most expensive metal in the world.
Specialists STS
Created in 2006 in the Joux Valley by Frédéric Saulcy and Thierry Mesnier, STS, which is part of the Acrotec Group (see our article Acrotec - Vertical integration in the supply sector), has become one of the leading enterprises for surface treatments in the high-end watchmaking sector. It employs a workforce of 110 on four production sites in Switzerland’s Watch Valley and Geneva. Its reputation in watchmaking has enabled it to diversify into the automotive, aviation and connectivity sectors. But its core business remains watchmaking, for which it provides numerous solutions for electroplating, varnishing, tribofinishing, heat treatments and decoration.
STS has collaborated with the University of Franche-Comté and EPFL in Lausanne on several projects, and is also one of the few companies in its field to have a large R&D department. Which undoubtedly explains the company’s far-sightedness regarding the inexorable rise in the price of rhodium.
A less spectacular innovation than certain mechanical follies that occupy the spotlight, but undoubtedly more fundamentally useful to watchmaking and the watchmaking industry as a whole.
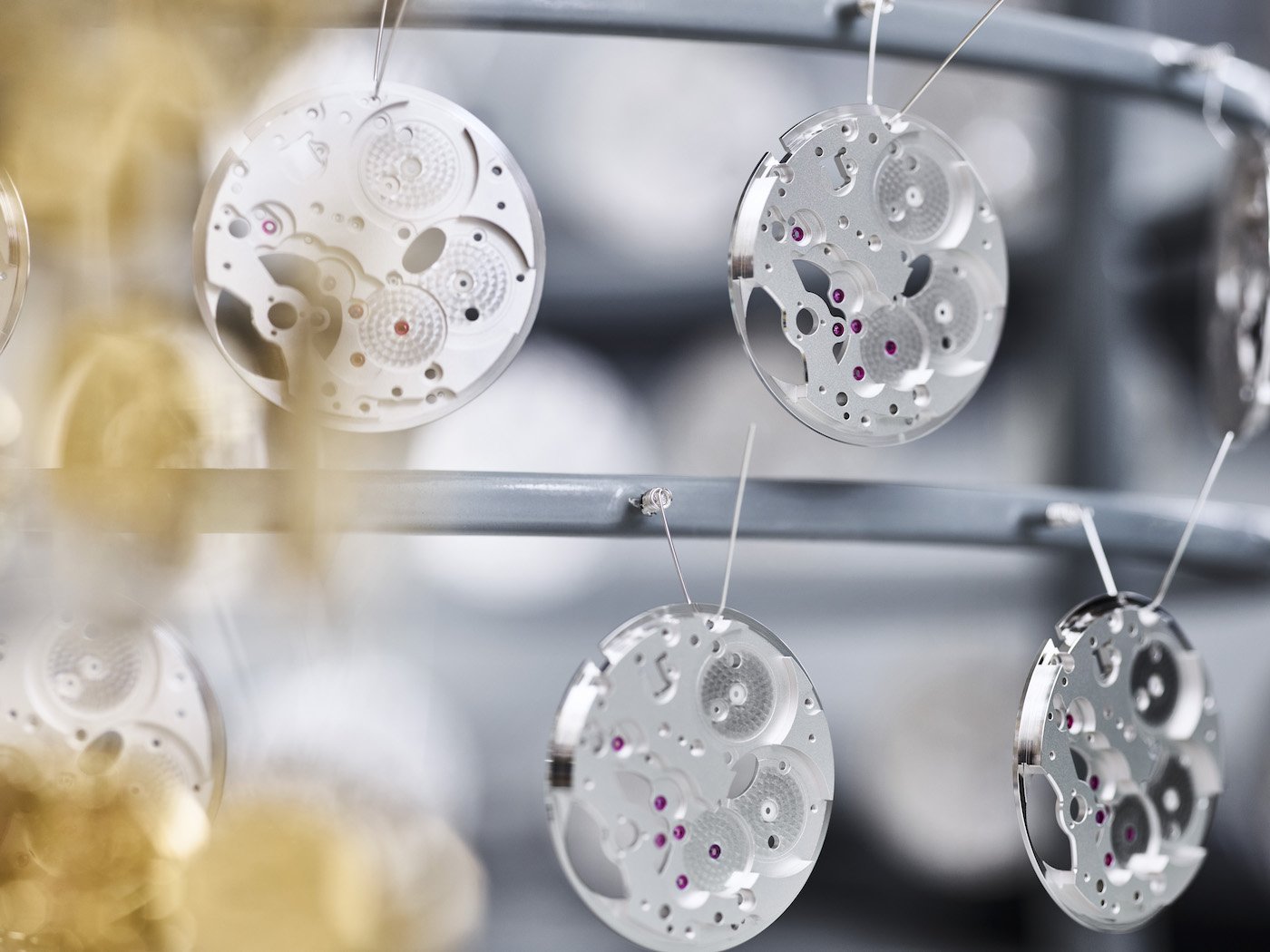
In search of an alternative
Historically, ébauches have been rhodium-plated for a very long time: its use dates back to the “peasant watchmakers”. But why? wondered the R&D managers at STS. “There seems to be no real technical necessity,” they explain. “But rhodium plating – also widely used in jewellery-making, especially for white gold – protects parts and provides a superb white finish. And rhodium bath plating is undoubtedly one of the easiest electroplating techniques.”
But now that rhodium has become the most expensive metal in the world, a genuine alternative had to be found.
More than a year of laboratory tests resulted in an innovative solution both technically and chemically: white platinum. Platinum and rhodium have got on well together, so to speak, for millions of years. Rhodium is physically related to platinum and always occurs with it in its natural state. It is also chemically combined with platinum in numerous applications. Back in 1896, the marriage of platinum and rhodium-plated platinum proved its worth in instruments designed to measure high temperatures. And that is just one example of the complicity between the two metals.
Rhodium is physically related to platinum and always occurs with it in its natural state. It is also chemically combined with platinum in numerous applications.
White platinum
Unlike rhodium, which is something of an endangered species, platinum resources are sure to last longer, as large reserves of it exist. Its unbeatable price – just over CHF 10 per gram compared to CHF 713 for rhodium (as of end October 2021) – make it a far more stable proposition in the medium term.
But that’s not all.
The result of a new, patented process, White Platinum by STS is composed of several metals, all from platinum mines. Developed by the R&D department, White Platinum provides a coating that is “just as white and shiny” as a rhodium coating, as well as being of similar thickness, up from 0.005-0.2μ to 0.1-0.2μ. Its hardness is 650HV compared to rhodium’s 850HV.
This new White Platinum coating can be reliably mass-produced and meets all watchmaking test requirements. It is compliant with REACH (the European regulation on the safety in the manufacturing and use of chemical substances in the European Union, which came into force in 2007) and resistant to Tropical Climate Testing (NIHS 96-50 climate and corrosion standard). In short, it seems to have everything going for it. Including its whiteness and shine.
Perfect timing
Some innovations arrive with a clap of thunder and a lightning flash. Others may arrive more modestly but be of genuine importance.
In a way, rhodium plating is part of watchmaking DNA. An ébauche without rhodium plating is but a shadow of itself. And so the fact that it is becoming unaffordable could, especially in these difficult times, damage the Swiss watch industry as a whole and its all-important volumes.
The exhibitors at the last EPHJ trade show in Geneva didn’t need to think twice. They awarded the 2021 EPJH Exhibitors’ Grand Prize to STS for their new White Platinum coating, which is comparable to rhodium plating on every score – aesthetically and technically – but at an unbeatable price.
It may be a less spectacular innovation than certain mechanical follies that tend to occupy the spotlight, but undoubtedly more fundamentally useful to watchmaking and the watchmaking industry as a whole.
Developed by the R&D department, White Platinum provides a coating that is “just as white and shiny” as a rhodium coating, as well as being of similar thickness.