nnovative materials are a reflection of the watch-buying public’s appetite for the non-traditional, as well as the vitality of the specialist companies that supply the industry, and which are behind the vast majority of these innovations. Our last in-depth feature on the subject was in 2018.
This article picks up from where we left off, covering the five years from 2019 to 2024. It reveals the two sides of R&D: on the one hand, the ongoing appeal of gold alloys, still synonymous with luxury and prestige; and on the other, an upsurge in composite, recycled, repurposed and even biosourced materials.
Extraordinary epoxy and diamond dust
Neoralithe is an epoxy-based composite from GVA Cadrans, a dialmaker in Satigny on the outskirts of Geneva. When Frankie Gerard bought the company in 2014, it employed five people. It now has a 25-strong workforce. Neoralithe was already part of the product range but its uses and possibilities have been considerably extended under Gerard’s directorship.
A complement to sapphire (which has its own applications), this hard composite can be given absolutely any colour in the Pantone colour chart. It can also be completely translucent or, conversely, totally opaque. The colours do not fade with time although the company is working to improve how its “opaque white" ages.
-
- Louis Moinet Time To Race with a two-tone Neoralithe flange
- ©Louis Moinet
GVA Cadrans has supplied Neoralithe to a number of watchmakers, including Jacob & Co., HYT and Louis Moinet. It can be used for a dial or even an entire case and, because it can be machined to thicknesses from one tenth of a millimetre up to several millimetres, Frankie Gerard points out the possibility of producing functional, moving parts from Neoralithe, “under certain conditions."
The company is a step ahead of demand, having developed technologies that brands have yet to explore. Neoralithe with suspensions of materials such as cement and even diamond is one (Patek Philippe is said to have given serious thought to the latter option, before changing its mind). Neoralithe with multiple coloured layers is another.
-
- Lab-grown diamond powder by Positive Coating, available in a range of colours
- ©Positive Coating
Over in La Chaux-de-Fonds, Positive Coating also has a material on its books which, as far as we can see, hasn’t yet been used. This busy company, which turns twenty this year, has developed a surface treatment which it describes as leaving a “precious veil” on a component. The process is simple enough: lab-grown diamond is ground to a powder then coated with an ultra-thin layer of colour (the company’s core activity) that lets the natural sparkle of the diamond shine through.
Organised chaos
Eighty percent of Vulkam’s business comes from the watch industry. The startup, which employs 35 people near Grenoble in the southeast of France, has developed what appears to be a unique technology for the industrialisation of amorphous metallic alloys, which have a disordered atomic structure. This may seem counter-intuitive. Surely something that has a regular arrangement of atoms – as do crystalline metals – is preferable to something “disorderly”?
“Except that’s never really the case,” comments Sébastien Gravier, who co-founded the business in 2017 (both founders have a PhD in metallurgy). “Breaks occur and these weak spots will spread more easily through a perfectly linear arrangement. A disordered atomic structure doesn’t have this regularity and is therefore ultimately much stronger.”
-
- Zirconium bezel
- ©Vulkam
Vulkam has resolved the technical challenges raised by the industrial production of these amorphous alloys, not least the importance of an oxygen-free environment. It offers two alloys of interest to the watch industry: one is zirconium-based, for external parts, and the other is nickel-based, for movement components.
-
- Movement component in nickel
- ©Vulkam
The company is already nearing maximum production capacity: a recent funding round raised €34 million which it will invest in a 3,000 square-metre industrial plant in France, scheduled to launch in 18 months’ time. The next will be in Switzerland, delivering technology and finished components to brands that also wish to benefit from the Swiss-Made label. All this takes place under the watchful eye of the French government, given that Vulkam already rolls out its solutions in medtech, aviation and aerospace, all highly strategic sectors.
Strapline
Watch straps are another fast-moving sector, largely driven by environmental concerns. This manifests itself in the repurposing of materials that were not originally intended for watchmaking. For example, CDK Maker is the inventor of Tanngreen. Made from grape pulp, a byproduct of winegrowing, this tannin can be used to dye various materials, including leather, in a palette of burgundy shades. The colours are stable and the technique has obvious environmental benefits.
Ictyos focuses not on colours but materials; it produces a range of marine leathers from fish skin. The company insists on the fact that no fish are farmed for this purpose and that it uses only waste products, mainly from food.
-
- Strap dyed with grape tannin
- ©CDK Maker
The company was set up in 2018 by three friends who met at engineering school and has a staff of nine in Lyon, France. It launched its first salmon leather in 2019, targeting B2B clients in leathergoods, footwear, furniture-making and, of course, the watch industry. The company doesn’t supply finished products (in our case, watch straps) but the raw material. As well as its expertise in salmon leather, available in a variety of colours, Ictyos works with other skins including sturgeon and trout. All its leathers are vegetable-tanned, which is a more environmentally-friendly process than chrome tanning.
Not that rubber (and related composites) have disappeared from the scene. Pascal Bourquard Jr., Biwi’s indefatigable CEO, is making sure of that. Based in Glovelier in the Swiss Jura, the company recently took the wraps off Superlite X: an ultra-light, ultra-durable, biosourced material that incorporates carbon fibres and super-fine glass microspheres (under 50 microns).
-
- The Superlite X composite by Biwi is 45% lighter than carbon
- ©Biwi
Pascal Bourquard Jr. describes this new material and its potential uses: “Superlite X has a density equal to one, which is less than that of water. It’s four times lighter than titanium, which has a density of 4.5, and 45% lighter than carbon. It can be used for all types of external parts, for example cases, crowns and bracelets, as well as movement components, building on solid partnerships with experts in the different branches. At this stage in development, there are no colour options but with time comes innovation…”
Go with the glow
Luminescence is another area where significant advances are being made. RC Tritec, which this year celebrates its 90th anniversary, is a leader in the field – you could even say that it is the field. The company, which employs 25 staff including five in research and development, is synonymous with innovation.
-
- X2 latest-generation lume by RC Tritec
- ©Tritec
Its Grade X2 pigment is up to 40% brighter than standard Super-LumiNova (SLN) with a longer afterglow – and the company is working on boosting this performance even further. Where colour is concerned, on the other hand, it seems RC Tritec has run the gamut, with lume in every shade under the sun. Or has it? Recent months have seen the company offer its clients (virtually the entire watch industry) a new product in the form of SLN that changes colour depending on UV exposure: up to three shades that customers are free to choose. RC Tritec has named this new technology UV PLUS.
-
- Tutti Frutti’ dial with luminescent hour markers in various colours
- ©Tritec
Current research focuses on structural SLN, which is not just a coating added to the component but the component itself: a luminescent monobloc. Imagine a dial featuring a three-dimensional skull, a mountain or a logo. Potentially, RC Tritec can produce any shape in any colour. Another area ripe for exploration is the addition of SLN powder to other materials. We’ve already seen Super-LumiNova mixed with carbon and ceramic, but there is still a way to go before particles can be incorporated directly into hard metals such as steel, titanium, platinum or alloys.
Noble bearing
Now let’s turn from the outside to the inside of the watch, and ball bearings. The technology has certainly come a long way since 1948 when the first ball bearings were developed for Eterna by the company that is now MPS. After doing away with the need for lubricant with the introduction, in 2004, of the X-Myrox ceramic bearing, MPS this year introduced next-generation Super-Myrox.
Still lubricant-free thanks to ceramic, this evolution provides improved shock-resistance and anti-magnetism thanks to materials innovation that replaces steel with a cobalt-chromium-nickel alloy.
Super-Myrox is compatible with ActiVib. Again thanks to materials research, in this instance a vibration damper in elastomeric polymer, MPS has developed a new generation of ball bearing that is 10 dB quieter and emits softer, pleasanter-sounding frequencies.
A case in point
The most noticeable, not to say palpable, advances concern materials for watch cases. Swatch and Omega sent the public into a frenzy with collaborations in bioceramic, a material composed of two thirds zirconium oxide ceramic powder and one third biosourced material derived from castor oil – a plant native to Africa and now grown in tropical regions around the world, including in China, India and Brazil.
Still, nothing glitters like gold, and these precious alloys have lost none of their appeal. Earlier this year, Audemars Piguet unveiled Sand Gold whose colour shifts between white gold and rose gold hues. This is an 18K alloy and not dissimilar to Chanel’s beige gold.
-
- Royal Oak in Sand Gold, a proprietary alloy from Audemars Piguet
- ©Audemars Piguet
More recently, in Milan, the Le Brassus brand premiered Chroma Gold, which applies sintering technology, a technique that was previously reserved for ceramic, to gold. The principle is to heat matter beyond its melting point (which is what potters do when they fire a piece in the kiln). To make Chroma Gold, different gold powders are combined in a mould and a powerful electric current is passed through it. This causes a rapid rise in temperature which, combined with mechanical pressure, “fixes” the camouflage pattern. And because this is gold, components can be classically finished.
-
- Audemars Piguet Royal Oak in Chroma Gold, combining three colours of gold
- ©Audemars Piguet
Meanwhile, Bianchet has unveiled its Hybrid Gold, a fusion of 18K gold, carbon and titanium powder which it says combines the luxury and brilliance of gold with the lightness of titanium and carbon. Titanium powder already features in an earlier proprietary alloy from the brand, Titanium-Dust-High-Density-Carbon, composed of 500 layers of carbon fibre infused with titanium powder between each layer.
-
- Bezel in Hybrid Gold from Bianchet
- ©Bianchet
Shine a light
Over at IWC, Ceralume is front and centre. The principle is straightforward enough: ceramic, in its basic state, is a powder. As is Super-LumiNova. The combination of the two, once fired and polished, gives a luminous ceramic case.
-
- Luminescent case and strap from IWC
- ©IWC
RC Tritec no doubt had a hand in achieving this result, which requires a perfectly homogeneous mixture with no accumulations of particles. It’s a safe bet that other colours are already in preparation, bearing in mind that Corum already released an Admiral’s Cup, in 2021, with a case in luminescent carbon.
-
- Carbon case with luminescent inserts on a Corum Admiral’s Cup
- ©Corum
Out with the old, in with the new
Ulysse Nardin turns old into new with Carbonium, a new-generation material that repurposes offcuts of carbon fibre used to manufacture aircraft fuselages and wings. Its inventor is a French company, Lavoisier Composites.
-
- Carbonium case at Ulysse Nardin, invented by Lavoisier Composites
- ©Ulysse Nardin
As is often the case with carbon composites, Lavoisier offers Carbonium combined with other materials such as gold or coloured pigments, but this startup (6 years old and 12 staff) goes further still. While its website gives examples of “off the peg” materials such as Carbonium, Pearlium and Stratalium, it will also produce alloys to order using (almost) any repurposed materials.
These can be leather, silicon, organic matter - just about anything provided the finished composite is robust, reproducible, machinable, economically viable, fit for purpose and sourced from recycled material.
-
- Carbonium case on the Romain Gauthier Micro-Rotor Skeleton
- ©Romain Gauthier
As well as Ulysse Nardin, Lavoisier has signed with Romain Gauthier... and numerous other brands whose names it is not at liberty to disclose. The company already makes 60% of its revenue in the watch industry. Currently, it handles all its own R&D and quality inspection, with plans to bring machining in-house as of next year.
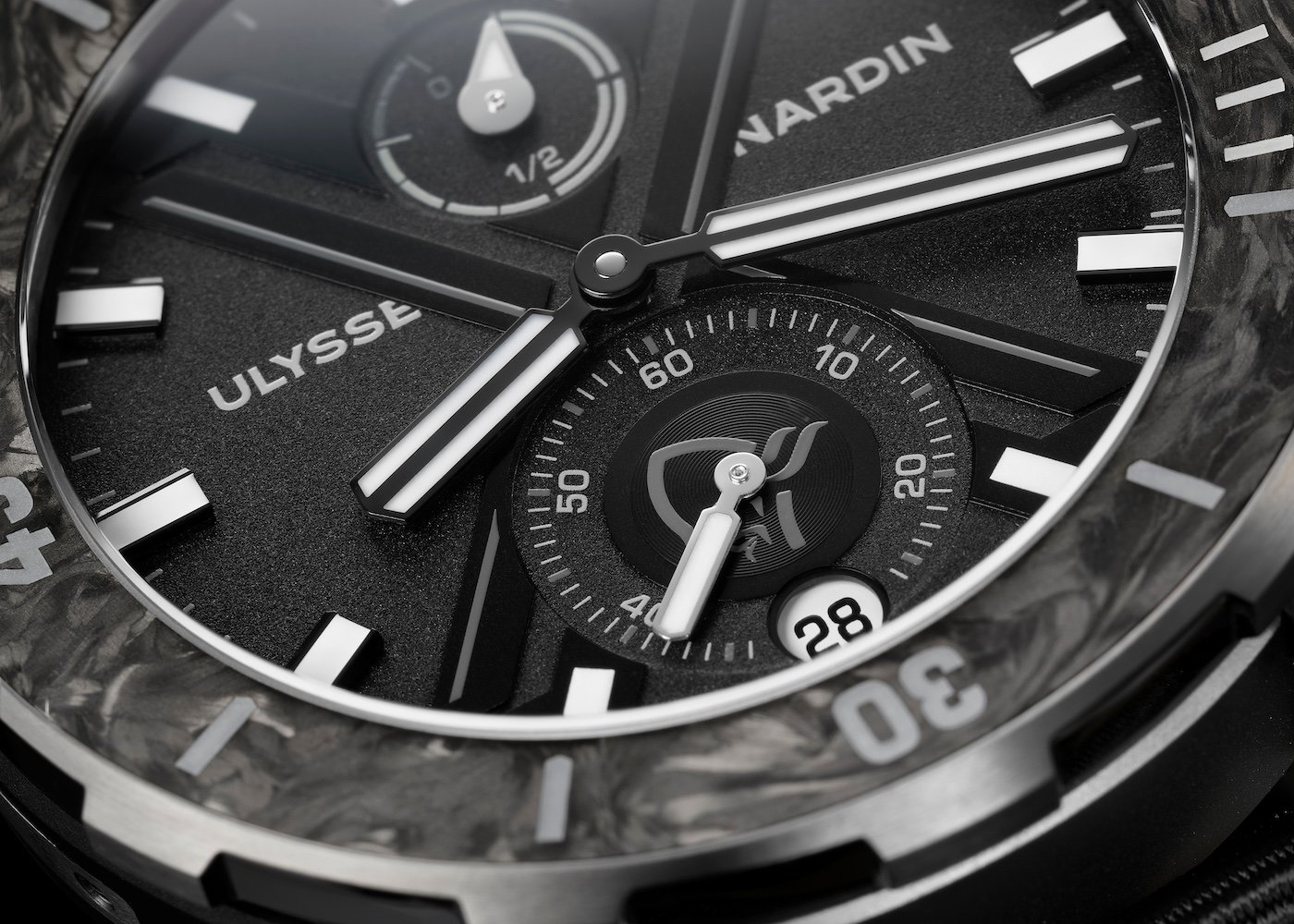