ulgari marks the completion of its redesigned and enlarged Saignelégier facility, which now brings watch case and dial production together under one roof – a unique setup in the industry.
With the addition of a new floor, the site has grown from 3,400 to 4,400 square meters. Its scale, along with the diversity of crafts it accommodates, enables Bulgari to fully leverage the synergies offered by vertical integration.
Driven by global enthusiasm for the brand, Bulgari is expanding its capacity for high-end case manufacturing by investing in cutting-edge industrial equipment, thus keeping pace with evolving market requirements. The upgrades focus on modernising production methods, fostering interdisciplinary collaboration, and enhancing versatility and multi-skilled training.
They also include optimised safety measures, improved work well-being for employees, and targeted measures to reduce the environmental impact of production. Notably, a new space dedicated to “Artmanship” – the fusion of Art and Craftsmanship – has been established at the heart of the manufacture.
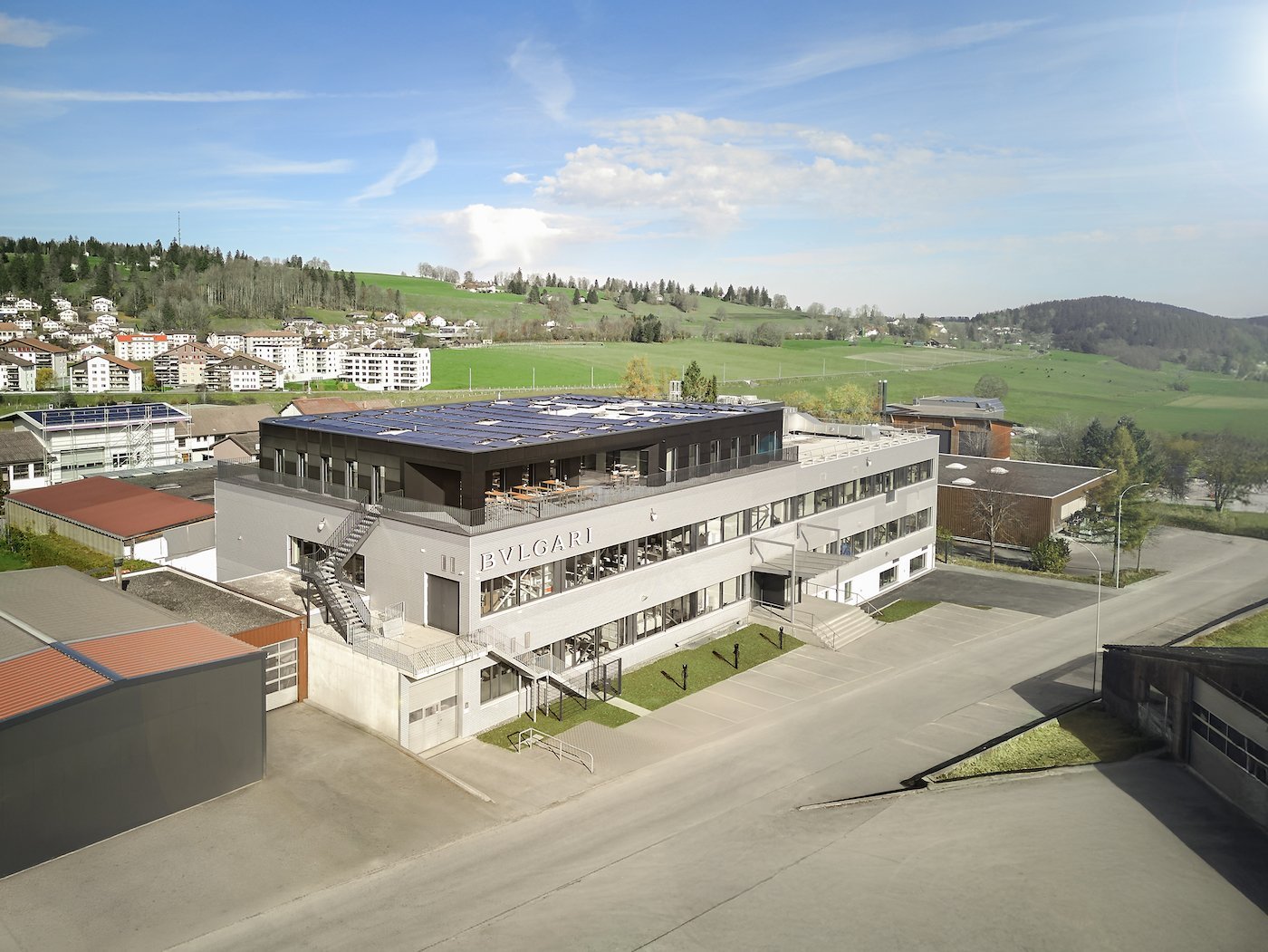
The success of Bulgari’s iconic collections – Serpenti, Octo Finissimo, Bvlgari Bvlgari, and its high jewellery watches – is driving a marked increase in demand for its dials crafted with traditional métiers d’art (artistic crafts and techniques). These dials, born from a convergence of rare expertise and artistic techniques, will now be crafted in a dedicated workshop for hardstone marquetry, peacock feather marquetry, gem-setting, and micro-painting.
This new space is characterised by its dynamic rhythm, responsiveness, and creativity. Even more so than in the rest of the building, where significant efforts have been made to improve the work environment, the new Métiers d’Art workshop ensures an atmosphere of silence and calm, required for artisanal crafts.
The Saignelégier Manufacture is equipped with a range of large-scale production machines, organized into workshops capable that can handle both small and medium production runs, coupled with high-end artisanal applications. This setup necessitated a redesign of the existing spaces to improve the flow of people and processes, the exchange of ideas, and ultimately, the level of production excellence. This combination of industrial and artisanal processes is being taken to the next level in Saignelégier, where, for example, lacquered dials that won’t tolerate the slightest presence of dust coexist with intricate hardstone mosaics.

Furthermore, the Manufacture now also features an additional floor with a staff restaurant and an outdoor terrace, along with a new wellness and recreation area. Indeed, the redesigned Saignelégier facility places the well-being of its 130 employees at the heart of its design.
The roof, façade, and parking areas have been redesigned to accommodate solar power generation. These solar panels supply 25% of the building’s energy needs. Coupled with redesigned workflows that reduce electricity consumption, this underscores the commitment to sustainability at Bulgari sites in alignment with requirements throughout the LVMH group.
The comprehensive renovation and expansion project at Saignelégier is part of LVMH’s ongoing investments in its watchmaking brands, naturally in Switzerland. As the world’s leading luxury group, LVMH has maintained a strong manufacturing presence in the Swiss Confederation for over 25 years, with no fewer than 15 sites dedicated to ten brands. Under the leadership of Frédéric Arnault, CEO of LVMH Watch Division, the division relies on these sites of excellence with a long-term vision, emphasising skilled craftsmanship, artisanal expertise, and especially Métiers d’Art (artistic crafts). This strategy of continuous investment secures a greater manufacturing independence for both LVMH and Bulgari through the integration of increasingly comprehensive expertise.
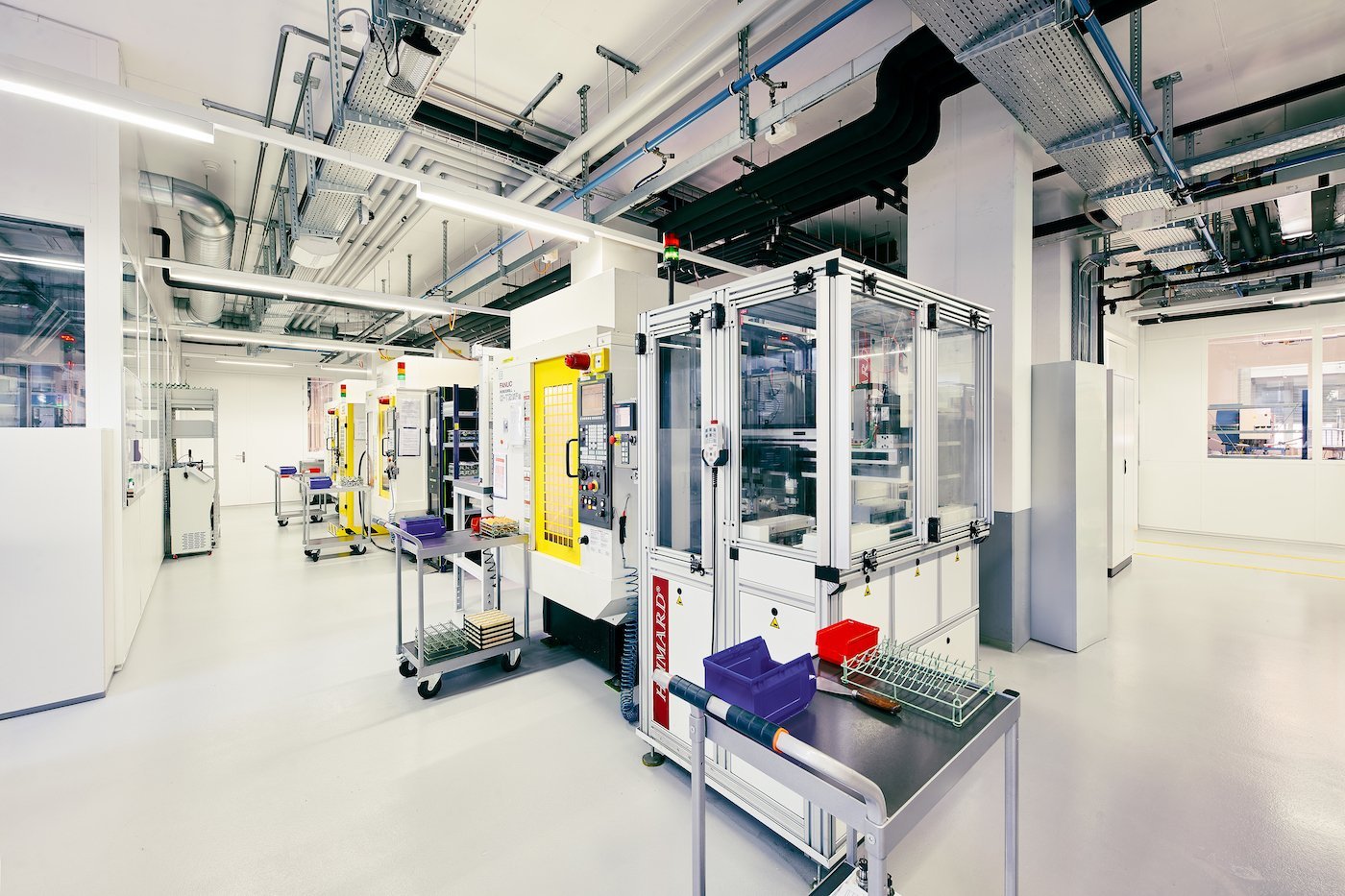
EXPERTISE
MANUFACTURING WORKSHOP:
- Programming
- 5-axis combined milling 3-axis milling
- Applique production
- Diamond polishing
- Turning
- Soldering
- Cutting
- Deburring
- Washing
FINISHING WORKSHOP:
- Manual polishing
- Automated polishing
- Satin finishing
- Buffing
- Grinding
- Sandblasting
- Laser engraving
- Laser decoration
SURFACE TREATMENT WORKSHOP:
- Electroplating (silver plating, gold plating, nickel plating, etc.)
- Varnishing
- Lacquering
ASSEMBLY WORKSHOP:
- Assembly (bonding, screwing, pressing)
- Water resistance testing
- Pad printing (decal application)
- Applique fitting
MECHANICAL WORKSHOP:
- CNC milling
- 3D printing