nnovation is not a product of luck or chance, but the result of persistent developmental efforts – ever since the invention of the self-powered illumination technology trigalight, it is precisely this understanding that has been shaping all processes and workflows at the Swiss microtech specialist. To keep carrying forward this innovational power over 50 years later, the company has established a new product development team, where classical methods are extended by agile ways of working. This, in combination with a new PolyJet 3DPrinter, will allow innovative ideas to hit the market faster.
True to the motto “innovators are those who innovate”, the mb-microtec ag and its brand trigalight – the world-wide leading producer of gaseous tritium light sources for the watch industry – decided to adopt new working structures and more agile processes. With the help of the newly established product development team, innovations can be more specifically targeted, and development times shortened.
Being a production company with a high degree of vertical integration means trigalight not only possesses the expertise, but also the infrastructure for the development and production of its gaseous light sources. All of the work processes from the first idea all the way to the practical application can be completely mapped out internally. To holistically align these processes with customer needs and to be able to integrate their feedback at an early developmental stage, a newly set-up product-development team was initiated – with new personnel and new responsibilities. This provides a dynamic link between production and sales. With the help of agile ways of working – inspired by concepts of design thinking – as well as customer and user integration at the earliest possible stage, product quality and time-tomarket should be optimized.
“With the new product-development team and their agile ways of working, we can work on multiple projects simultaneously. The goal isn’t only to save time, but to recognize early on, in cooperation with our customers, whether a product idea suits the market demands. Consequently, we don’t just innovate more, but also gain a more thorough understanding of if and how we can get these innovations successfully to market entry. The results of our internal structural changes are of quantitative, but mainly qualitative nature,” Karsten Richter, Head of New Business and Product Development, says.
She draws a positive conclusion after the first year and a half: “After a bit of initial skepticism, we’re now fully convinced that this restructuring was the absolutely right decision in order to continue to position ourselves as leaders in both innovation and quality.”
While being known for their self-powering illumination technology trigalight, the Swiss innovator is constantly on the look-out for new fields of application. To find and develop new ideas, as well as react quickly to market trends, the team works in shorter intervals. This allows them to set clearer short-term goals speeding up decision making.
“Getting from the original idea to the first prototype used to take us about a year and a half. Now, we can do it within ten to twelve months,” Remo Pfaff, Product Development Engineer, states. “Most of all, we’ve felt a significant increase in the knowledge transfer within our team, and to the production and sales teams. Individual, static ‘information-ponds’ have turned into a continuous ‘information flow’. Our colleagues learn from the start to work solution-oriented, and that’s also felt by our customers, who in turn perceive us as solution provider even more.”
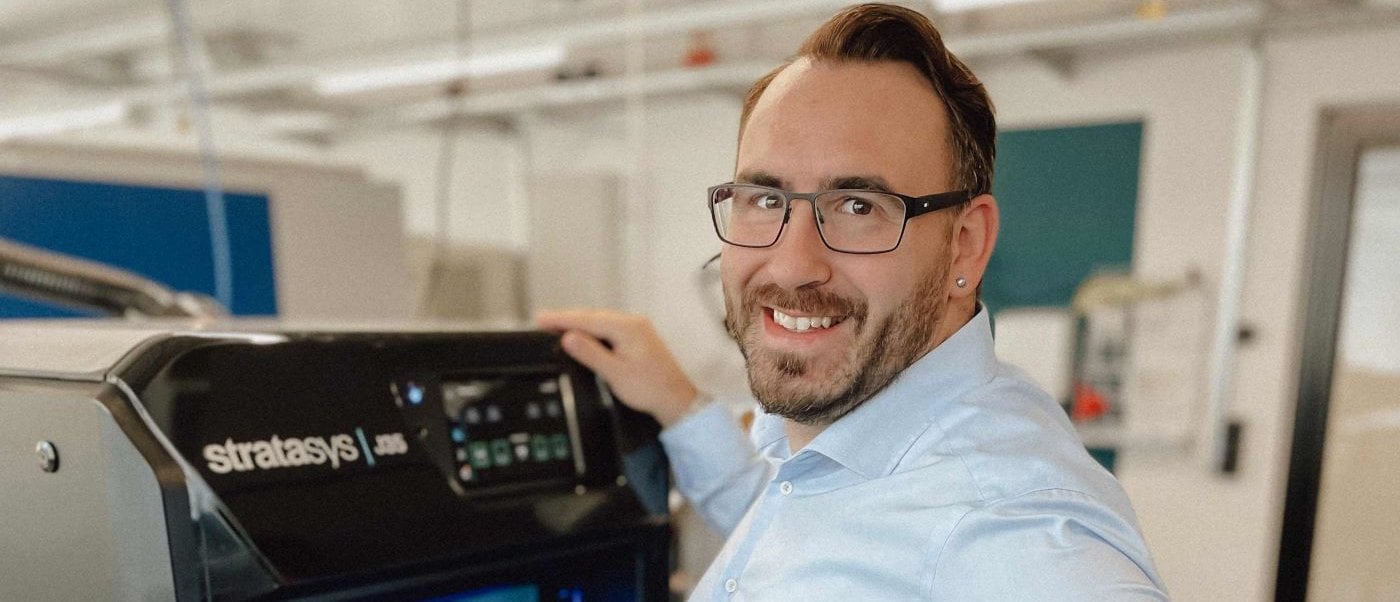
trigalight is a unique light solution that can illuminate even finest components of a watch, such as the pointers, indices and gear wheels for years. Thanks to its variable use and customizability, safety and minimal size, trigalight offers true additional value not just for the readability of the watch, but also for its design. To give potential customers an idea of just how wide its field of use is, the team has begun to use a PolyJet 3D-Printer. Matter of expense: a mid-five-figure sum. But this investment pays off, and the device has quickly become an essential tool for every-day work. It allows the product-development team to produce and test gadgets more quickly, running them through a series of reality checks and trial and error to speed up development. Instead of showing the customers drawings and sketches, they can now present them with prototypes in different shades of gray, transparent, or full color as well as various material appearances.
“The transformation from paper to prototype provides a more creative, emotionally gripping and precise exchange with our customers,” Karsten Richter explains. “When we work with a watch maker to develop a new model, we can quickly create a prototype identical both in size and color to the original model, including a visualization of the later positioning of trigalight capillaries on pointers and indices. What used to take three to four months can now be done overnight, thanks to the 3D-printer.”
Ever since the invention of trigalight, the mb-microtec ag has been driving the continuous development of its self-powered illumination technology as well as its own infrastructure. In 2018, the company moved to its new, Minergie-certified, headquarters, which boasts the world’s most modern tritium monitoring system, a climate-controlled production floor, and extensive safety measures. After years of development, the company also introduced the first and only tritium recycling plant of its kind in December 2020, which allows for a closed life cycle of all its products. Never content, this pioneering spirit ensures that the company never rests on its laurels, powering forward through investments in infrastructure as well as the constant scrutinization of its own processes.